A guide to commissioning and maintaining tank fill valves
Tank fill control valves are commonly applied across a range of applications including water supply in commercial agriculture, irrigation systems, and fire control.
The issue
Once a tank fill valve has been selected and installed in accordance with manufacturer instructions — there are several ways to ensure its optimum performance. Michael Jacobsen takes us through the commissioning, maintenance and troubleshooting of hydraulically operated tank fill valves.
Commissioning a tank fill valve
When a tank fill valve has been accurately chosen for an application, there is little experience required to commission it. By following the steps below, you will be able to maximise a trouble-free operation without adding to installation time:
- Ensure the isolation ball valve installed on the side of the main valve body is open. This is positioned just prior to the Y-strainer.
- The needle valve leading into the valve bonnet is fully closed, then opened with 1.5 to 2 turns.
- The isolation ball valve on the valve bonnet, that has the float tube attached to it, must also be fully open.

When turning on the water for the first time, the valve should be open. This will allow water to flow through the tank — even if the tank is full. This is because the valve control chamber is not pressurised. It will take a short while for the control chamber to pressurise, and the valve to close if the tank is full.
The valve will remain open if the tank water level is below the shut-off level.
Releasing air from the valve control chamber is also recommended. This can be done by loosening a nut on the tube connection fitting at the highest point.
Water will start to escape after only a turn of the nut — allowing the air to release.
Once the air bubbles stop coming out with the water, the nut can be retightened.
Maintaining a tank fill valve
Tank fill valves that are installed in buildings are generally working with clean water. This means that they do not often require regular maintenance. There may be a building code or regulation that stipulates periodical maintenance be conducted, and in these circumstances, maintenance can be made simple and practical. Maintaining tank fill valves usually involves replacing diaphragms after an extended period of operating time.
Troubleshooting
There are a few circumstances where the common hydraulic tank fill valve is unable to function within an application. Examples of this include:

- The valve does not open when the tank level has dropped.
- The valve does not close when the tank is full.
Not opening:
When a valve doesn’t open in response to a drop in the tank water level, it is because something is preventing the valve control chamber from de-pressurising. Settings to check are:
- The needle valve is set as instructed under Commissioning.
- The isolation ball valves are open.
- The float assembly is functioning correctly. When in the open position, water should be discharging through the vent hole in the float assembly. If this doesn’t occur, then either the float assembly is faulty, or there is a blockage between the valve and the float. This can be quickly checked by loosening the nut on the tube fitting at the isolation ball valve. This step will de-pressurise the valve control chamber and cause the valve to open.
Not closing:
Majority of people experiencing issues with tank fill valves, cite problems with the valve failing to close once full. The most common reason for this problem is a result of debris, particularly stones, being trapped in the valve. This is especially the case for systems that don’t have strainers or stone traps installed. Settings to check are:
- The needle valve is set as instructed.
- The isolation ball valves are open.
- The float assembly is functioning correctly. When in the closed position water should not be discharging through the vent hole in the float assembly.
- In the event that the float assembly cannot be reached, and on the basis that steps 1 and 2 have been completed; a substitute test is to close the isolation ball valve leading to the float. This will cause pressure to accumulate in the valve control chamber and close the valve. If the valve does not close, then the valve internals should be checked for trapped debris.
If you would like further information or manuals for the tank fill valve, please visit the product page to learn more.
If you are interested in utilising this product in your next project, get in touch with us via our website, or contact your local sales office — we’d love to hear from you.
Make enquiry
Online Enquiry Close
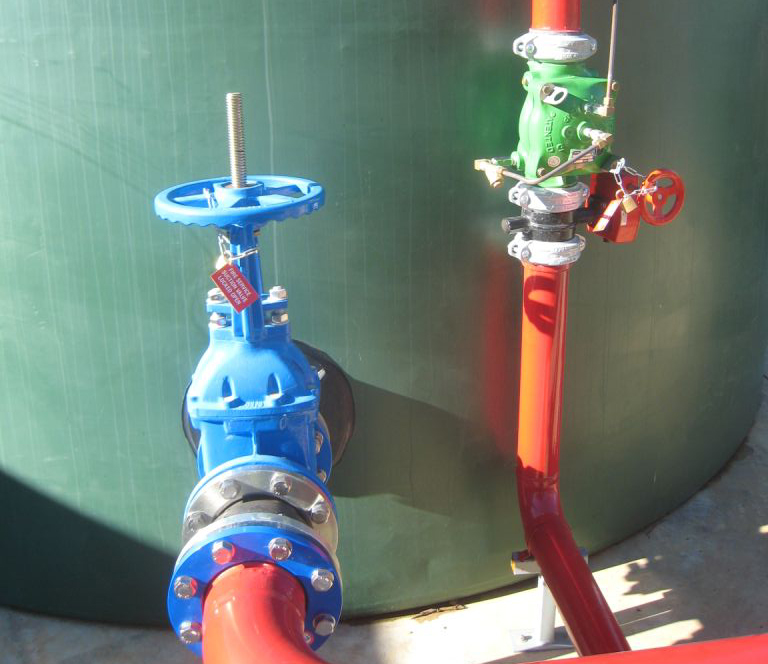
Tank fill control valves are commonly applied across a range of applications including water supply in commercial agriculture, irrigation systems, and fire control.
The issue
Once a tank fill valve has been selected and installed in accordance with manufacturer instructions — there are several ways to ensure its optimum performance. Michael Jacobsen takes us through the commissioning, maintenance and troubleshooting of hydraulically operated tank fill valves.
Commissioning a tank fill valve
When a tank fill valve has been accurately chosen for an application, there is little experience required to commission it. By following the steps below, you will be able to maximise a trouble-free operation without adding to installation time:
- Ensure the isolation ball valve installed on the side of the main valve body is open. This is positioned just prior to the Y-strainer.
- The needle valve leading into the valve bonnet is fully closed, then opened with 1.5 to 2 turns.
- The isolation ball valve on the valve bonnet, that has the float tube attached to it, must also be fully open.
When turning on the water for the first time, the valve should be open. This will allow water to flow through the tank — even if the tank is full. This is because the valve control chamber is not pressurised. It will take a short while for the control chamber to pressurise, and the valve to close if the tank is full.
The valve will remain open if the tank water level is below the shut-off level.
Releasing air from the valve control chamber is also recommended. This can be done by loosening a nut on the tube connection fitting at the highest point.
Water will start to escape after only a turn of the nut — allowing the air to release.
Once the air bubbles stop coming out with the water, the nut can be retightened.
Maintaining a tank fill valve
Tank fill valves that are installed in buildings are generally working with clean water. This means that they do not often require regular maintenance. There may be a building code or regulation that stipulates periodical maintenance be conducted, and in these circumstances, maintenance can be made simple and practical. Maintaining tank fill valves usually involves replacing diaphragms after an extended period of operating time.
Troubleshooting
There are a few circumstances where the common hydraulic tank fill valve is unable to function within an application. Examples of this include:
- The valve does not open when the tank level has dropped.
- The valve does not close when the tank is full.
Not opening:
When a valve doesn’t open in response to a drop in the tank water level, it is because something is preventing the valve control chamber from de-pressurising. Settings to check are:
- The needle valve is set as instructed under Commissioning.
- The isolation ball valves are open.
- The float assembly is functioning correctly. When in the open position, water should be discharging through the vent hole in the float assembly. If this doesn’t occur, then either the float assembly is faulty, or there is a blockage between the valve and the float. This can be quickly checked by loosening the nut on the tube fitting at the isolation ball valve. This step will de-pressurise the valve control chamber and cause the valve to open.
Not closing:
Majority of people experiencing issues with tank fill valves, cite problems with the valve failing to close once full. The most common reason for this problem is a result of debris, particularly stones, being trapped in the valve. This is especially the case for systems that don’t have strainers or stone traps installed. Settings to check are:
- The needle valve is set as instructed.
- The isolation ball valves are open.
- The float assembly is functioning correctly. When in the closed position water should not be discharging through the vent hole in the float assembly.
- In the event that the float assembly cannot be reached, and on the basis that steps 1 and 2 have been completed; a substitute test is to close the isolation ball valve leading to the float. This will cause pressure to accumulate in the valve control chamber and close the valve. If the valve does not close, then the valve internals should be checked for trapped debris.
If you would like further information or manuals for the tank fill valve, please visit the product page to learn more.
If you are interested in utilising this product in your next project, get in touch with us via our website, or contact your local sales office — we’d love to hear from you.
Make enquiry