Air valve with anti slam for surge protection
Network outages can cause a range of issues in your system, including water hammer. Reduce the impact of power failure by incorporating anti-slam valves for optimal flow.
The issue
When a pump is switched off, and is located on flat topography, column separation can occur. Column separation occurs when air valves draw large amounts of air into a pipeline, which is followed by fast release of air as the column re-joins.
As this can happen very quickly, standard combination air valves can generate water hammer when the large orifice charges up.
The solution
There are many methods to reducing the impact of water hammer, including the addition of surge vessels, pressure relief valves—or more commonly a specialised air release valve such as the CSA anti-slam air valve.
CSA air valves automatically release air pockets and can admit large volumes of air during power loss, preventing any negative pressure from occurring. CSA’s anti-slam air valve has the capability to break the vacuum caused by water hammer, this allows air to enter the pipeline unrestricted. This airflow is discharged as the returning wave of water hammer travels towards to pump at a slower calculated flow rate.
This controlled, slow air discharge uses the air bubbles (caused by water hammer) as a shock absorber to dampen the return wave—this prevents the retuning column of water from slamming against the closed pump check valves.
To watch an animation of this, visit the Bermad Youtube Channel to learn more.

Valve installation and sizing
The valve should always be installed on the discharge side of the pump check valve. This could be either on the common manifold, or as close as possible to the bend prior to the pipe re-entering the pipeline.
Typically, the valve is always isolated to the pipeline by use of a butterfly or gate valve to ensure access for valve maintenance.
In relation to choosing a valve size, it is important to understand the flow rates of the pumping station. It’s always best to check with our engineering team, as the pipe material and pressure rating plays an important role in ensuring that your system doesn’t exceed vacuum ratings of pipe under air inflow calculations.
In contrast, being conservative and over sizing the air valve can have the effect of not dampening the return wave sufficiently. Our recommendation is to send the following details to our team for accurate sizing and support:
-
Water quality.
-
Number of pumps in the system.
-
Pump design and motor speed (e.g. Turbine pump at 4 pole 1440 rpm).
-
Individual pump flow rate and discharge pressure.
-
Pipeline diameter, length, material and PN rating.
We’re here to help
If you’d like further design assistance or additional information such as animations, data sheets, manuals and CAD drawings, visit our online product page.
Our team of dedicated staff are always prepared to find a solution. We offer extensive product information and engineering data on our product pages, which are available here.
If you require on field assistance, get in touch with our team via our live field support tool, or contact our team online.
Make enquiry
Online Enquiry Close
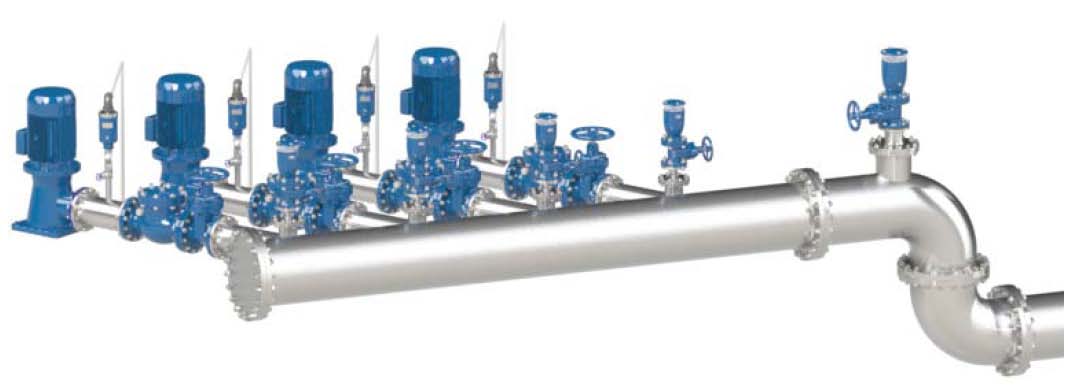
Network outages can cause a range of issues in your system, including water hammer. Reduce the impact of power failure by incorporating anti-slam valves for optimal flow.
The issue
When a pump is switched off, and is located on flat topography, column separation can occur. Column separation occurs when air valves draw large amounts of air into a pipeline, which is followed by fast release of air as the column re-joins.
As this can happen very quickly, standard combination air valves can generate water hammer when the large orifice charges up.
The solution
There are many methods to reducing the impact of water hammer, including the addition of surge vessels, pressure relief valves—or more commonly a specialised air release valve such as the CSA anti-slam air valve.
CSA air valves automatically release air pockets and can admit large volumes of air during power loss, preventing any negative pressure from occurring. CSA’s anti-slam air valve has the capability to break the vacuum caused by water hammer, this allows air to enter the pipeline unrestricted. This airflow is discharged as the returning wave of water hammer travels towards to pump at a slower calculated flow rate.
This controlled, slow air discharge uses the air bubbles (caused by water hammer) as a shock absorber to dampen the return wave—this prevents the retuning column of water from slamming against the closed pump check valves.
To watch an animation of this, visit the Bermad Youtube Channel to learn more.
Valve installation and sizing
The valve should always be installed on the discharge side of the pump check valve. This could be either on the common manifold, or as close as possible to the bend prior to the pipe re-entering the pipeline.
Typically, the valve is always isolated to the pipeline by use of a butterfly or gate valve to ensure access for valve maintenance.
In relation to choosing a valve size, it is important to understand the flow rates of the pumping station. It’s always best to check with our engineering team, as the pipe material and pressure rating plays an important role in ensuring that your system doesn’t exceed vacuum ratings of pipe under air inflow calculations.
In contrast, being conservative and over sizing the air valve can have the effect of not dampening the return wave sufficiently. Our recommendation is to send the following details to our team for accurate sizing and support:
-
Water quality.
-
Number of pumps in the system.
-
Pump design and motor speed (e.g. Turbine pump at 4 pole 1440 rpm).
-
Individual pump flow rate and discharge pressure.
-
Pipeline diameter, length, material and PN rating.
We’re here to help
If you’d like further design assistance or additional information such as animations, data sheets, manuals and CAD drawings, visit our online product page.
Our team of dedicated staff are always prepared to find a solution. We offer extensive product information and engineering data on our product pages, which are available here.
If you require on field assistance, get in touch with our team via our live field support tool, or contact our team online.
Make enquiry