Unmatched deluge valve performance through diaphragm design
Learn about the Torrent 400Y diaphragm actuated deluge valve, including key design features and evidence of performance in harsh hydraulic conditions.
Deluge valves are required to offer a wide variety of functions—from ‘on-off’ to performing accurate downstream pressure regulation—sometimes with extremely high flows and high inlet pressures acting upon them.
While diaphragm actuated deluge valve body design is important, the actual valve’s diaphragm design and construction is crucial in:
- The valve’s capability to resist the large forces created by the flows, and
- Possible large pressure reductions acting across the valve.
Designing the 400Y for robust performance
The Bermad team looked at the possibility of harsh hydraulic conditions and designed the 400Y to best handle these conditions. Bermad looked at the Weir Pattern Diaphragm valve as a starting point for designing the 400Y Torrent valve. Bermad then decided to use the positives of this design, being it’s simplicity, having only 3 components, being the valve cover, body, and valve diaphragm, and how to minimise the weaknesses of the design, being the unsupported, single thickness diaphragm sealing on a small weir seat .
The team at Bermad have carefully considered all components of the Torrent 400Y for optimal performance in extreme demand hydraulic conditions.
The improved solution
The Torrent 400Y rubber diaphragm consists of two sections.
The upper section is a flexible, fibre-reinforced diaphragm. The bottom section is a solid fibre-reinforced plug, with a steel disc vulcanised within the plug. The diaphragm is also hydraulically balanced and peripherally supported by the valves’ body to avoid tension in the diaphragm.
The diaphragm upper section
The thinner, fabric-reinforced upper section consists of a rolling diaphragm which is continually supported by the valve’s body.
This section’s main purpose is to provide the regulating sensitivity required to achieve high accuracy pressure control, while also providing low differential pressure closing capabilities.
The lower diaphragm section
The lower section of the diaphragm is a solid reinforced plug. It is designed to resist the effect of high forces which will attempt to drag the diaphragm downstream, as well as resisting the forces that will attempt to inflate the inner surface of the diaphragm outwards due to pressure from the valve control chamber.
Additionally, the plug always remains in the one plane, ensuring that it always seals against the 360-degree seat machined into the valve’s body
What this means is that you get Diaphragm strength where it is required and sensitivity where it is required.


Understanding the potential impact of high-level hydraulic conditions
There are a number of Diaphragm Actuated Deluge Valves currently available in the Fire Protection market which are based on the Weir Type design.
The Weir pattern valve consists of a single thickness diaphragm and a valve body which has a weir-shaped seat that the diaphragm is pushed against to seal by the valve control chamber pressure.


In high flow situations or conditions with high pressure differentials, the inherent design of the deluge valve body—combined with the single-thickness diaphragm—can impede valve operation or contribute to lowered valve endurance.
Additionally, the diaphragm has a small area of support by the valve’s body to help resist the large forces which drag the diaphragm towards the downstream when high flows and large pressure drops occur at the valve. Also when there is high pressure in the valve’s control chamber, there is the possibility that the pressure can expand the diaphragm which—when combined with the drag forces—may cause problems in sealing and diaphragm distortion.
What can happen to these valves in extreme demand applications?
The following tests demonstrate what can happen when a Weir pattern valve is subjected to high level hydraulic conditions.
Testing was conducted on a 150mm diameter Weir-style Solenoid operated Deluge valve which also had a pressure regulation function.
These tests were recently performed in the testing facilities of Bermad manufacturing plant in Israel.
The valve was tested in the following Hydraulic conditions:
Dynamic testing:
- Upstream pressure: 2000kPa
- Downstream regulating pressure: 350kPa
- Flow rate: 120 litres per second
Static test:
- 2000kPa in the valve control chamber
- Zero pressure upstream
- Zero downstream pressure
Testing procedure:
Testing consisted of two periods of 1-hour dynamic testing, followed by five days of static testing, before a further 1-hour dynamic test.
The diaphragm progressively degraded with full failure at the conclusion of the third dynamic test.

2000kPA static pressure showing diaphragm deformation

Diaphragm failure
About the test results
It is important to note that these results are based on one manufacturer only and highlight the result of testing under very harsh hydraulic conditions. We are at no stage implying that Weir-pattern deluge valves are not suitable for use when general hydraulic conditions are acting upon them.
Bermad has performed a similar series of tests on the 400Y Torrent valve, and even subjected it to much higher flow velocities and pressures than detailed above. The valves have passed all these tests to meet the demands of high end operating conditions.
To view the operation of the Torrent, view the following video :
Make enquiry
Online Enquiry Close
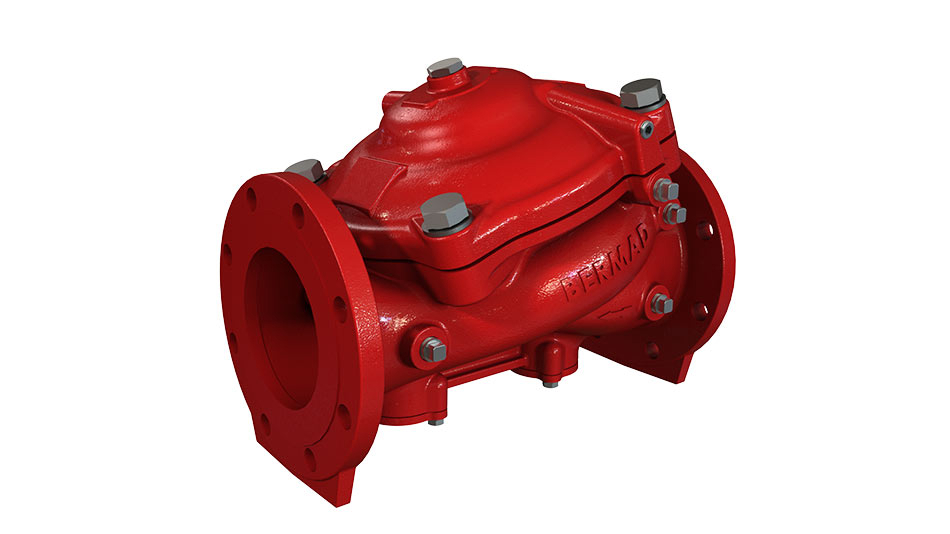
Learn about the Torrent 400Y diaphragm actuated deluge valve, including key design features and evidence of performance in harsh hydraulic conditions.
Deluge valves are required to offer a wide variety of functions—from ‘on-off’ to performing accurate downstream pressure regulation—sometimes with extremely high flows and high inlet pressures acting upon them.
While diaphragm actuated deluge valve body design is important, the actual valve’s diaphragm design and construction is crucial in:
- The valve’s capability to resist the large forces created by the flows, and
- Possible large pressure reductions acting across the valve.
Designing the 400Y for robust performance
The Bermad team looked at the possibility of harsh hydraulic conditions and designed the 400Y to best handle these conditions. Bermad looked at the Weir Pattern Diaphragm valve as a starting point for designing the 400Y Torrent valve. Bermad then decided to use the positives of this design, being it’s simplicity, having only 3 components, being the valve cover, body, and valve diaphragm, and how to minimise the weaknesses of the design, being the unsupported, single thickness diaphragm sealing on a small weir seat .
The team at Bermad have carefully considered all components of the Torrent 400Y for optimal performance in extreme demand hydraulic conditions.
The improved solution
The Torrent 400Y rubber diaphragm consists of two sections.
The upper section is a flexible, fibre-reinforced diaphragm. The bottom section is a solid fibre-reinforced plug, with a steel disc vulcanised within the plug. The diaphragm is also hydraulically balanced and peripherally supported by the valves’ body to avoid tension in the diaphragm.
The diaphragm upper section
The thinner, fabric-reinforced upper section consists of a rolling diaphragm which is continually supported by the valve’s body.
This section’s main purpose is to provide the regulating sensitivity required to achieve high accuracy pressure control, while also providing low differential pressure closing capabilities.
The lower diaphragm section
The lower section of the diaphragm is a solid reinforced plug. It is designed to resist the effect of high forces which will attempt to drag the diaphragm downstream, as well as resisting the forces that will attempt to inflate the inner surface of the diaphragm outwards due to pressure from the valve control chamber.
Additionally, the plug always remains in the one plane, ensuring that it always seals against the 360-degree seat machined into the valve’s body
What this means is that you get Diaphragm strength where it is required and sensitivity where it is required.
Understanding the potential impact of high-level hydraulic conditions
There are a number of Diaphragm Actuated Deluge Valves currently available in the Fire Protection market which are based on the Weir Type design.
The Weir pattern valve consists of a single thickness diaphragm and a valve body which has a weir-shaped seat that the diaphragm is pushed against to seal by the valve control chamber pressure.
In high flow situations or conditions with high pressure differentials, the inherent design of the deluge valve body—combined with the single-thickness diaphragm—can impede valve operation or contribute to lowered valve endurance.
Additionally, the diaphragm has a small area of support by the valve’s body to help resist the large forces which drag the diaphragm towards the downstream when high flows and large pressure drops occur at the valve. Also when there is high pressure in the valve’s control chamber, there is the possibility that the pressure can expand the diaphragm which—when combined with the drag forces—may cause problems in sealing and diaphragm distortion.
What can happen to these valves in extreme demand applications?
The following tests demonstrate what can happen when a Weir pattern valve is subjected to high level hydraulic conditions.
Testing was conducted on a 150mm diameter Weir-style Solenoid operated Deluge valve which also had a pressure regulation function.
These tests were recently performed in the testing facilities of Bermad manufacturing plant in Israel.
The valve was tested in the following Hydraulic conditions:
Dynamic testing:
- Upstream pressure: 2000kPa
- Downstream regulating pressure: 350kPa
- Flow rate: 120 litres per second
Static test:
- 2000kPa in the valve control chamber
- Zero pressure upstream
- Zero downstream pressure
Testing procedure:
Testing consisted of two periods of 1-hour dynamic testing, followed by five days of static testing, before a further 1-hour dynamic test.
The diaphragm progressively degraded with full failure at the conclusion of the third dynamic test.
2000kPA static pressure showing diaphragm deformation
Diaphragm failure
About the test results
It is important to note that these results are based on one manufacturer only and highlight the result of testing under very harsh hydraulic conditions. We are at no stage implying that Weir-pattern deluge valves are not suitable for use when general hydraulic conditions are acting upon them.
Bermad has performed a similar series of tests on the 400Y Torrent valve, and even subjected it to much higher flow velocities and pressures than detailed above. The valves have passed all these tests to meet the demands of high end operating conditions.
To view the operation of the Torrent, view the following video :
Make enquiry