Designing a pressure reducing station in water supply
Play Video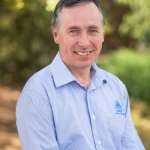
Published on
Presented by Colin Kirkland
Join Bermad Water Technologies Air Valve and Product Manager, Colin Kirkland, in this technical training seminar on designing a pressure reducing station in water supply. In this presentation, learn more about:
- Determining correct information to enable sizing of a station
- The logic to determine size and number of valves required
- Sizing reports and implementing in a design
- Considerations for above or below ground installation
- Installation techniques and pitfalls
- Inlet strainers, air release valves and downstream pressure relief valves
Content
Transcript
Hi, welcome to this Bermad technical seminar. Colin Kirkland is my name I’m one of the engineers at Bermad water technologies. The purpose of this technical training seminar is we believe it’s going to be useful for any designers, operators, or engineers who are designing a pressure reducing station in water supply to share 30 odd years of experience, which we have in Australia of designing good and bad stations.
And to be able to go into many of the aspects, which might assist you in the design of a station.
So with that, let’s get started and get into the content which we’re going to provide here. One of the things that we found is really essential before designing a station is really to get the correct information to enable us as a manufacturer, to really design the right size of valve, the right station and the right sort of design.
So we’re going to talk a little bit about some of the information that we really think we need from you for to enable us to get that design done correctly. Once we’ve got a lot of that information, we’re going to talk a lot about the sizing logic that we use and why we use a single valve or multiple valves for that type of design.
And we’ll go into that in a little bit more detail. We’re going to show you some of the software which we use, which really takes out the risk of selecting that particular valve size. So, the software which biomed has, has had many years experience and really gives us a lot of confidence in what we’re going to do.
And we’ll share that with you and show you how we use that to as best band. sizing developers and with part of the solution. So part of the critical nature of any designers really thinking about, do we, how do we design the station? Do we put it above ground below ground? And we’ll talk a little bit about the pros and the cons, and this will maybe give you and help you in your selection process when you’re going into the actual detail of how the final design looks.
The thing that we found is really important is that designers, a lot of the time have a great idea of what they want, but this seminar is based on talking to operators, talking to people who do maintenance on the units, plus people who are designing. So all these different people have a different concept and what they think is useful and practical.
And then we’ll discuss some of the pitfalls relating to some of the main tech maintenance on the valve, because the, one of the critical things is, of course, it’s great to design it, but how are we going to work on. And is it practical to work on it in its present design? So we’ll talk a little bit about that too, as well.
We’ll talk about some of the components external to the actual valves, which have an impact on the performance of the pressure reducing station. One of the things we’ll talk about is do we need a strainer before the valve? Is it something that’s needed? Is it practical? And we’ll talk about the pros and cons of that.
When we design a station, one of the things that impacts the performance on the valve many times is air. And we don’t like air in any pressurized pipeline. So we’re going to talk a little bit about the design of the air valve we should suggest to use in particular designs and where to locate them and how to get the best performance out of that design too.
And also, there’s a, when you look at data catalog, sometimes you will see a pressure relief valve down stream; and we’ll talk a little bit about the pros and cons of using one of those and some of the design implications of putting one of those in a network.
Okay.
So let’s start from the scratch. If someone was coming to Bermad and they were asking us, to assist in the sizing and the selection of the valve, what is some of the information that we actually need to enable us to start the ball rolling? So the first thing is it’s a little bit about the general description.
So what I’m getting to there is this water supply, is it drinking water? It’s going to be in a major city? Is it’s going to be a roll water pressure reducing station providing treatment plant? So we want a general idea of the application description and to know what it is we’re dealing with before we start.
The water quality is really critical. So there’s different things which we do, if we are doing one for drinking water, or as opposed to maybe river or dam water that’s running to a treatment plant, or it could even be potentially treated effluent or recycled water pipeline station, which has different aspects to as well.
So we want to know a little bit about the water quality that we’d expect in that station. But we’ll make it right down to the hydraulics, there’s a lot of information which really helps us give a really comprehensive selection on the valves. First thing is to really understand what we talk about it as cumin. We talk about the minimum overnight flow rate. So we’re trying to understand if this was a brand new subdivision we’re trying to understand will the flows go to zero or is there some leakage in the network where it might get down to 2, 3, 4 liters a second. We want to know what the minimum flow rate will be through the station. We want to know the average daily flow rate. So what works, we’ll go into this a little bit more depth, but we’re trying to understand the nominal average flow through the station is 20 liters a second. And that happens usually at nine o’clock during the day. And we want to get a bit of an idea. So I wanted to get the 75 80 percentile of where the valve is going to be operating in the bulk of its time.
We also need to know what the maximum daily flow rates and the maximum daily flow rate is going to be. So we have to consider that in the highest demand times. So that could be summer. It could be right in the peak of summer when everyone’s watering the gardens and there’s a lot of usage of water where people showering and living.
So we want to know what the valve has to cope with at its maximum too, as well. And that’s really quite critical when designing a pressure reducing station. That’s not only feeding reticulation, but it’s commercial buildings and everything else. There’s what we call a fire flow.
Let’s talk about in a city and a city arrangement that could well be that on those very extreme days that we need the ability to also be able to cope with a fire condition, or it could be a rural installation where we are out in the country and there’s potential in a one in two or three yearly event and we have a bushfire or something else where all of a sudden the potential flows could rise to a very high level. And we’d like to get a bit of an understanding of what that potential fire floor requirement is, indeed that’s part of the design itself. Now, it’s all good to know what the flows are that we need and the pressures today, but we’re not designing for today; we are designing for today, but also for the future.
So in a world where the population’s rising all the time and we’re getting more and more people, we want to know potentially what the maximum design flow is going to be in 10 years, 15, 20 years, 30 years, because one of these stations is really being designed for the long term.
A typical life of a PRV is, 20 to 40 years if it’s maintained and operated correctly. So we want to take or ask the question. If you’ve got a snapshot idea of what we think you might think that flows might be in the future. And what that really helps us do is really determine what the design will look like, whether we need to put redundancy or think about the sizing and how we design it for the future, going forward.
We’ve spoken about flows, so know about pressures. So pressures are really important. We really need to understand the maximum inlet pressure. So this is the maximum head that we’re expecting to see at the inlet side of the valve. Really important for us to know from cavitation and performance and sector too, as well.
We want to know the average pressure. So this is roughly what the pressure is going to be through the day, so we can understand how the valve is going to perform and the lowest inlet pressure. So that might happen in the very hot days where you have excessive flow is going to everywhere and the head drops through the head loss in the network. So we’re interested to know that lowest pressure to as well. And of course the most important thing for a pressure reducing valve is what is your downstream pressure you want? In many instances, we call that the P2P pressure. And pressure, reducing valve only cares really about one thing and that’s maintaining that pressure.
The thing about the downstream pressure is that it’s a fixed, it’s a fixed situation and that’s what the valve cares about. Maybe in your design, you may want to modify that pressure. You may want to be able to have different pressures at different times of the day. So if you’re planning on doing pressure management or having a step situation where you want to change that pressures, it’s give us that information and that helps us look at the design of the valve.
Okay. So let’s go into a little bit more depth about the flow rates that I was talking about. It’s really important to understand this graph that we’re looking at on the left here. The horizontal axis is showing us the 24 hour clock and the vertical axis there is showing us the flow rates and liters per second.
This is not exact, but this is a typical thing of what we would generally find in a water reticulation network, where we tend to see that peak flows tend to happen in the morning when people are waking up they showering, they’re having breakfasts. The demand is quite high in the network at that point.
And as people go to work or start the daily lives, the flow is going to drop off. You might get a little peak in lunchtime and then, potentially we might tank to see some peaks again later in the day. So this is what a typical peak or demand will look sort of thing. This is what we’re talking about, trying to understand what that minimum overnight flow will be.
We can see here, it’s down less than three liters a second, during the day, we’re expecting the flows to get up to on 16 odd liters a second. So this is what we mean by the average daily fluoride. The fire flow this isn’t a given this isn’t a fixed while it’s 20% more than the maximum. It’s whatever the design of the system is going to be. If it was a rural network where I we’re out in the country, and there was a lot of fire hydrants, this could be 30, 40% more than the maximum flow, or if were in the city, it could be 5% more, but that’s up to you to advise us where you think that requirement might be.
Because one of the things that is really essential for a building or a fire work is that if you don’t have sufficient pressure you can achieve the firefighting results that you want to want to achieve. So if we haven’t considered this in the design of the valve, and all of a sudden the valve is choking point that we simply can’t deliver that, the ramifications are not good.
So it’s important to speak about this now and here we can see on the graph, we can see the red line where potentially it’s mirroring the average daily furrows, but it’s just showing what potential we might actually get to as a maximum. Now, future daily flows; So this is a bit of pie in the sky sort of thing, but let’s think about areas that, say down at holiday making areas by the ocean a lot of people, as they’re retiring may want to move to the ocean and those are the developments in those areas tend to grow considerably. So the thing is here, we’re trying to get an idea of what the flows are going to be today, but what they’re going to be in 10, 20, 30 years time from now, and most planning, councils and water companies have a good idea of what they think potentially it might be going forward in the future.
And this is really important to know tonight. It’s not absolutely critical when we design a station, we don’t design it so much in the age that it’s going to fall over if we have a 20% increase in flow, but it’s just important to know it. So for example, looking at this picture on the right hand side, we can see a 50 millimeter trend on the left-hand side where that does 99.9% of the flows. But in the in the event that we have a fire or we have a situation where they want to fill a reservoir on a rare event or something else, it’s not going to keep up. So the trend on the right-hand side is going to supplement that and enable us to continue that flow. And then the bypass and middle might be that we don’t want any pressure reduction in the manual fire, we just going to open this and whatever.
So it’s giving you an idea of what we really need to consider. So they, these are the flows that we’re talking about, which I spoke about in the start. And if you’re in any doubt with any of this, the whole thing is just to communicate with bare mind. And it’s not that we can’t. Provided design without that, but it’s handy to know and as good future planning too, as well.
So let’s talk a little bit about pressures. Usually a pressure reducing station might be on a dedicated pipeline, or it might be on a T branch coming off a dedicated pipeline, supplying a DMA. But one of the things that we find, if we look at the graph on the left here is that it’s very important for us, not just to know what the maximum inlet pressure is going to be, but we want to know what the inlet pressure is going to be at varying flows. Now why that’s important, if we look at this graph here, we can see that this is the pressure $that we’re tracking of the inlet side of $this pressure, reducing valve. And we can see that at very little flow, we have 80 to 90 meters of water pressure, but once we get up to full design flow, where the pressure is dropping to 30 meters.
Now the valves are going to perform differently at different pressures. They are going to potentially be in a cavitation zone if they’re in very high differential pressures. So we don’t only just need to know the maximum, but we really need to get an idea of what that range is going to be throughout the flows. Now, most modeling engineers can come up with some of that information. So we’re talking about head loss and pipes and networks to give us an understanding, because if we don’t know this, then it can be a problem in the event that we do have a rare event that we don’t have the energy for the valve to operate, and we can’t get the demand.
So it’s important to get an idea of the range of the inlet pressures.
What do we do at Bermad we’ve gathered all this information and one of the things, I’ve been with them for more than 21 years, is that Bermad has always prided itself on a lot of industry experience and really understanding how the valves operate the Bermont sizing software, which we have.
Doesn’t only give us a snapshot of how the valve is going to perform in one flow, but we can, as you look at this pitcher on the left-hand side here, you can see the software. We’ve got a a pressure reducing valve we’re trying to size in, in, in 150 millimeters. And we’re looking at 10% of the time, the flow is going to be in this consideration, but the 70 percentile will be here going to be 20%.
We have the low flows on the left. So what the sizing software does for us and what it does for you as a potential client or user or designer, is it gives you a snapshot of exactly how that valve is going to perform today. We can do that for those floors today. We can do it for future floors. We can do it for design flows, and it gives you a good idea of what the valve was actually designed for.
So if we think potentially 15 years down the track, and we’re seeing that the design that we put in really wasn’t performing well, let’s go back to what we considered was the original information we were given to actually design it. Okay. So we can see here that we’ve got a maximum flow of 50 liters, a second.
We’re actually finding we’re actually peaking at 80 today. We haven’t considered this so we can, it’s a really good snapshot of an idea to tell us how it’s going to perform. It’s going to tell us clearly here, the percentage of the valves open. So we look at this particular case on maximum flow of the valve is 45%.
We’re getting a very good idea on the noise level. So now this is a really critical point of any design because if we are designing a pressure reducing station site in the country, or it’s in an area that’s hasn’t got houses or it’s maybe cause some factories rind on it and it’s making a small amount of noise.
That’s fine. But what if in 10 years, time is a lot of houses around us and these valves are generating 70 to 80 decibels of noise at night and it’s keeping homeowners and everything else. There is a problem. So a lot of engineers and water authorities want to know potentially what the noise levels are going to be.
And we could ask them all of the time, the software that gives us a very good snapshot of what that’s going to be. And why that’s important is that it helps us, or helps you as designers to say what am I going to do about the noise? How are we going to put in the pitt to suppress the noise. They put acoustic enclosures around it or are we going to do other things hydraulically that can reduce those effects?
And there’s things that we can do inside the valve with the trim. There’s a multitude of things. The point is that this is a really good snapshot and we provide this reports to you, the designers or the users, so that you can get an idea and have confidence that we’re not guessing. And it’s not just a case of “yeah, it’ll be right.” these are the facts. This is how it’s going to work. So this is good engineering data for you. This is part of anything that we do in selecting a valve. So we’ve selected a valve. We want to know a little bit about the network that it’s providing. So is it what we call a single feed supply with a bypass?
So in other words, is there only one pipeline that is supplying this network of pipes and why we want to know that, is that at some stage, we have to maintain this valve. Now the majority of the maintenance, which we do it doesn’t require a valve to be taken off line. It can be done quickly and simply and easily with a several maintenance techniques without taking the valve offline, but there is for any part of the product, there is an opportunity where we may have to remove the valve internals and inspect the valve seats and the internals and the V ports, ect. That means taking the water offline. Now, why is that important? If it’s a, if it’s an authority where we’re supplying buildings, factories, and homes, we do not want to switch the water supply off. So, we may have to put a bypass valve in here that says we’re going to put a standby valve. That’s going to enable us to maintain the water supply and still do the maintenance on the valve safely. Or it could be a single feed supply. That’s filling a reservoir. And can we take the valve offline for four hours to check the internals?
Absolutely, that’s fine. So these are the things we’re going to ask you is that a single feed supply? And if so, then we’ll consider possibly putting a bypass in or giving you some suggestions of how we can design a system that doesn’t interrupt the water supply. Now, many authorities tend to have a multiple feeds.
So this could be a situation where we’re providing in a city St or here or in a part of a development as a pressure reducing valve to fill it, but maybe six kilometers away. We have another feed that supplies that from the south end of time-saver the north end of time. So we call us a multiple feed supply into a network.
Now, why is that important for us to know as a designer? The water will always take the least former existence feeling this DMS. If we know that the bulk of the water is going to come from the north and only salvage comes from the south, it gives us an idea how to proportionalize the valve and how to make sure that we get the best performance side of it.
We don’t want 90% of the flow going through one valve and Tampa St through another. Or we can even have situations where we have a hundred percent of the water going through one. And the other valve is redundant, not doing anything. And it only comes in a rare event. And that can be an issue. So this is what we mean.
If we’re asking you, is it like a single feed supply, or is it a multiple feed supply going into the network that you’re providing? Okay. Let’s take a snapshot in time. Let’s go back 20 years ago. When we used to provide a single feed supply, if we look at this picture on the right hand side, this is a pressures using station for drinking water, and we can see the three valves at the bottom.
And here we have a 50 millimeter, a one 50 millimeter and a three hundreds. And this was supplying a drinking water network in a holiday type region. And why did we have the three valves? In the early days, a lot of the valves really they didn’t have the capability of working in a very wide full range, but today is very different.
You can see here on the discharge of the three valves as a pressure relief valve heading off to the left there, just to safeguard network two as well. But most valves in the early days had what we called a flat disc or a flat seat. And what we mean by that is that the valve really doesn’t have a great potential to work at very low flows.
It works in a nice, comfortable band, and it doesn’t tend to work terribly well at exceptionally low flows, but for. The last 20 or 30 years, we have a whole variety of different components we can put inside the valve, like the V port plugs here, which give us the ability to run down to zero flows, many instances.
So we also have today in high differential pressure conditions, we have cavitation cages like shown here. We have a single cage or a Juul cage, and these are components, which basically say, look, instead of having a design, like we see on the right hand side here where we. Three valves to really cope with the floors and the pressure demands and everything else.
It might be a situation where we can have a demand with one few hundred millimeter valve to do the entire situation. So things have changed. There is a, obviously bear Matt is one of the leading manufacturers in the world of diaphragm, actuator control of, and they’re constantly developing their products, and today, as well as being Australian standard approved, this product really has the ability to work in a very wide band.
So designs today can look very different to what we had in the past. And this is just gives you a bit of an idea of the old and the new here to see what can be done in instances like that.
If we think about, I’m going to use a practical example here. This is the logic of a single feed supply with a bypass. So here, we’re looking at, if you look at the picture on the right to start with, we have a hundred millimeter valve in the distance there with a strainer before it, and it’s running into a water network and we have a smaller 50 millimeter valve before it.
So the issue, and if we look to the the flow rate range on the left-hand side of the draft that we’ve got there, we can see the 24 hour clock there with the floor capacity, and we can see the the flow rate vertically and in the vertical there, unit two as well. So one of the things that we don’t like to do in a pressure reducing valve is have a valve that’s redundant and doesn’t actually operate.
Now, what we mean by that is, is that a lot of, if we looked at this picture on the right hand side, let’s just say, for example, the 50 millimeter valve, which handles the low flows can do 100% of the daily flow. And the a hundred millimeter valve only supplements the flow in the event of a fire or in a rare event that might happen once or twice a year.
The issue with that is, is that we can have dead water sitting behind that a hundred millimeter valve, the water quality engineers, don’t like dead water going into the main, so we can get discoloration. We can get low chlorine contents and it can also affect the performance of the valve control valves like to operate.
So one of the things which we do we, the other thing is that we don’t like to drive the small valve to very high flow rates. We want these valves to last for 20, 30, 40 years. So we know that if we have parallel valves, one of the things we don’t like to do is to run exceptionally high flow rates through the small valve.
Why? Because it’s going to weigh, it could be subject to capitation and it’s not good for the long term of the. At the same time, we don’t want the the valve and the left not to operate. We actually want it to continue for water quality reasons, like I mentioned before and reasons of reliability.
So if we look at the graph on the left here, what we tend to do is we say look let’s limit the flow through this 50 millimeter network to 6.5 liters a second. And let’s ensure that every day we get that a hundred millimeter valve to actually open the highway. We do that is we add a mechanical flow stem to the small valve.
That’s probably a little difficult for you to see in the picture, but then the 50 millimeter valve is a brass dam in the middle in there. So what we’re doing is we’re basically saying. What we want to do is keep both the valves active every day that keeps the water quality. Good. Keeps the velocity through the small velvet, a conservative level, and ensures that both valves are designed for the long term and they really work well.
So a lot of the time we discuss with you the possibilities and the designs of incorporating something like this to ensure that we give a good design station that works well today, six months, 12 months, and in 20 years. And this is some of the logic which we use in some authorities when it’s just a single feed type supply.
Okay. Now, one of the things is that I mentioned before about having multiple valves coming into one location. And I did mention before that sometimes what we don’t want is to have a pressure reducing valve that doesn’t operate that it’s not that it’s going to fail, but it has more potential to if it’s sitting.
Doing nothing for one year, two years of his time, it’s a problem. I look at this particular installation here. This was a pressure reducing valve that was used as a bypass around a large reservoir. So in this network we had water supply filling a reservoir, and the reservoir was like a brake pressure tank and what it would gravitate her through the reservoir, out through the network.
But if there was a problem with the tank in that they have to put some divers in there, or do some maintenance on the tank and take the tank off line. You wanted this pressure reducing valve to operate and to maintain the same pressures at the time was used to. So if we look at this particular design, you can see the water flowing from left to right.
We can see the the inlet butterfly valve, the control valve. And then we see that the second butterfly valve on the downstream side, which has closed into the network now. Before they are, you can see a T piece with a hydrant. So one of the things that we might do and I’ve learned through many authorities is that it’s good to test the valve before you bring it online.
So what an operator might do here is they’ll put a hydrant in here before they put it online. They’ll open the hydrant, the allow water to flow, which means we’re getting rid of the dead water. We’re testing the valve operation. We’re stroking the valve and opening and closing it. And we’re insuring by modifying the position of the hydrant that the PRV is operating as it’s designed.
So it’s a good way to be able to test the valve before bringing it online. So there could be a lot of valves for a variety of reasons that are going to be redundant in the network are needed in the emergency situations. This is a really good way of a design by putting a single hydrant in there, or a test valve to test it, before bringing it online. And I just thought this was a non-ideal picture to demonstrate that and to show it. So sometimes that’s a good thing to incorporate if you have a redundant PRV.
Okay. So we’ve now looked at the hydraulic data on the valves were selected. A valve of subjects suggested a multitude of different valves or a single valve. What do we do with it now? Do we put it above ground? We put it below ground? What are the pros and cons? And I’m going to go through a little bit of that process to, to give you some decision-making ideas, which operators and designers have given us in the past that might make your life easier to design one of the.
So let’s talk about above ground installations. So we can see a couple of pictures here where we have one valve out in the open. I’m supplying a rural part of the country, supplying a pressure reducing station. And then we have another pressure reducing station in a brick building, still above ground. It’s above ground, and it’s providing it there. So, why would you consider putting it above ground? Let’s talk about some of these things.
First thing is that to an operator who has to maintain the valve it’s easy to work on it. If it’s above ground, I can get access to it, I’m not in a confined space in a pit, I can easily get one person who can come to the valve and operate and work on it.
One of the things which is exceptionally important from an operator safety point of view is that in many of the water authorities which we work at, we have permits required for confined space entry. And in some cases when we put valves below ground and pits, we have what we call a confined space, a certificates required. And what that may mean is that yes, I’ll be able to have an operator go down into the valve pits with breathing apparatus. I need to have two operators upstairs, one with a harness, one, just monitoring the device to, to safeguard the person that’s in the pits. But if we are…today, we don’t have a lot of operators working on these valves. If we’re above ground, we can have one operator come to the valve and work on it safely, no confined space. It can get to the valve simply you can see it as easy to get to. So it’s efficient. It means that we have one operator doing maintenance on the valve instead of three. So it becomes a financial decision and stuff too, as well. And we don’t need that. My personal preference is if you can put it above ground, do it because it’s so much better for the operators.
Let’s talk about the cons and the advantages here. As I mentioned, when we were suggests suggesting the type of valve is that we can do different trims to the valve and different designs that have different decibel ratings. But at the end of the day, regardless of that, if you’re working on a high differential installation, it could be that the noise level is just not suitable. Now we can see the top picture here is out in the open. There’s no houses nearby, a little bit of noise isn’t gonna affect anything. I know, for example, when I took this picture of the bottom one, it’s right next to houses.
So, what they’ve decided to do here is to put it inside a brick building to suppress some of that noise, keep the weather off the valve and stuff too, as well and make it… noise suppression is something to consider. One of the disadvantages potentially, if it’s outdoors, if you’re in a frost prone region where you’ve got to very cold temperatures that could drop below zero, we could have issues with frost.
Now there’s frost is a whole other topic, but it depends what part of the country you’re in. Obviously Australia is a very big place. But if we were done in Tasmania or we were up in Darwin, we very different aspects to talking about frost. So that’s one of the things to consider vandalism, if we’re above ground and the valves out in the open, as we can see, you’ve got a cage around it just to keep people away, but kids being kids, they might do some vandalism to the velvets is a critical valve. We don’t want people to damage it, so it could be something we want to consider. It’s not always possible, of course, to be above ground. We could be in the very center of a big city where we simply just haven’t got the room and the practicality to put it there.
And for many councils and for many water companies, it might not look so good to have valves above ground and sitting there if it’s in the country and it’s not offending anybody, no big deal. But as a rule of thumb, we find a lot of valves even in big cities that are above grind, but in many cases that are below ground.
So let’s now talk a little bit about below ground installations. There’s many reasons, and I’ve got some different pictures here at the end, defining a few.
So we can see the top picture there is a pressure reducing station in a valve pits, concrete level. We can see the ladders going down there so we can see what the operator has to do.
The middle installation they are showing. The installation and a very large city, it’s compact, it’s quite tight. It’s got a lot of other components in it and stuff too, as well. So it’s tightened the bottom one later, of course, showing a valve, being some merits, which happens frequently. So let’s talk a little bit about some of the advantages.
The, if it’s below ground, typically the pipe is majority of the time is below ground. So if the pressure reducing station can break into a single or multiple train below ground, it means it’s avoiding a lot of the Bends, elbows, thrust blocks, and everything. Having to come from a combined above ground.
It keeps it quite simple in other words. In many cases, that’s more practical for where it actually is. If it’s below ground, and let’s say the transfer pipeline is on a major highway or crossing a highway or on a road or on a pavement, for example, it can be that it can be underground and they can be pits across the top where traffic can pass across it.
Now that’s practical in that it saves costs by not having to offset the PRV. But of course it can be a disadvantage in th,at when we come to maintain it, it’s a problem for access to as well. But it usually means that it can be done quite simply and easily to that degree. It can reduce costs.
What we mean by that is, is that it’s avoiding all of those thrust blocks, it’s avoiding bends, tees, coming above ground air valves and other components. But I guess one of the key reasons why a lot of the operators will consider putting it below ground is not so much cost related, but it’s noise related.
When I was demonstrating on the sizing program, we can see that at different conditions and the different percentages of the valves open or different hydraulic conditions, we can get a varying level of decibels of the noise of the level of the valve. So by putting in a valve, we know through experience that especially if it’s got Gaddy covers and it’s in a concrete pit, it can suppress a lot of that noise. And that’s important if it’s going to be in a residential area where you’re going to want to make sure that noise isn’t affecting the residents close by.
Let’s talk about some of the disadvantages here. Some of these disadvantages, the information that I’ve gathered has come from operators, it’s come from users and some designers and stuff too.
So within many of the water companies in order to go into a below ground pit, each water authority or council has a varying definition of what we call a confined space and a confined spaces where it’s potentially dangerous for an operator.
So we want to put a gas detector down there. We want to put an operator down there with a harness. We want to have somebody upstairs holding the harness and somebody spotting you at the same time. So to do a simple maintenance on a filter station, every six months means I need three people. So it can be costly from an ongoing operators perspective.
The ongoing costs are expensive. If I’ve got three people coming out twice a year to do that, instead of one, there’s a cost associated with that. The other thing that I’ve heard from a lot of the water companies is I’ve got an American seed breakdown situation. It’s two o’clock in the morning. I’m on call. I’ve got to race out to this PRV station. I’ve got to go down in the pit. Let’s look at the picture on the top of the page there. We can see the yellow lighters going down.
These environments, usually below grinder damp and their weight and the potential for slippage and someone falling and hurting themselves is potentially there. I’ve been down in hundreds of outfits. And it is, you have to have your wits about you, but if you’re on your own and you potentially damage yourself and hurt your head it’s a, it’s an issue. So there’s an health and safety issue to consider going in there to we’re talking to all health and safety.
It’s a damp environments where potentially you can get spiders, snakes. I’ve been to many of those cases where, red back spiders or something like that, or, if you’ve got a Brown snake in there, that’s very dangerous to an operator and you can’t see them. Now, it doesn’t mean you can’t get those snakes and spiders above ground, they tend to find dark places to hide and all that sort of stuff. So it’s just means that we’ve got a, an open a more dangerous environment from an operators. From an actual perspective of, I need to maintain the valve, if we look at that middle picture, for example, here, we’ve got pressure transmitters, we’ve got motorized pilots, we’ve got electrical cables, we’ve got water and it’s a very confined space.
This is a 200 millimeter valve and we can see here, it’s a very tight confined space to actually get into, to work. And a lot of the time a designer will say, look, come Colin, can I have the side of the valve and a hundred millimeters of the concrete wall and you can say look, you can but from an operator’s perspective, he’s going to get his arm in there to get spanners, to remove the actuator and it’s not always easy.
So it’s really quite challenging. And when you’re down in a valve pit here and you’re trying to work on everything and you’ve got a mixture of electricity and water, and it’s certainly the risk of, and I’ve been in this actual situation where pits have flooded before, something’s gone wrong and a fitting is broken or a dead bolt has given way or something, and it can be very dangerous for an operator to as well above ground. Yes, you still have those same issues, but you’re not in a confined area that can be dangerous to an operator. And look, the bottom picture is a little bit of tongue in cheek, but this is the reality of sometimes what happens if the valve pits is not fully sealed. If it’s open at the open greeting at the top of the valve can submerge. Now, it’s not that the valve can’t work when it’s fully submerged, but obviously it’s not ideal. We can get corrosion, we can’t see the valvem, we can’t work on it, we have to get pumps in to empty the pits. It’s not great. So what I’ve been able to demonstrate there is a little bit of the decision-making on above ground or below ground, whether this practical or it’s good and.
Different person’s gonna have a different perspective on it, but there is the best of both worlds. So what some people have said to us as Colin, we want to have the valves in a pit. In this case, we can see in this picture the pressure reducing station was all prefab by one of our good contractors in stainless steel with Victaulic joints to make it very easy to get in and out.
But the, a water company didn’t actually want the operators to go into the valve pits to do the regular maintenance. So what they’ve actually done here, if you see to the left-hand side, they’ve actually put the controls or the components that require the frequent maintenance right at ground level.
So on this particular case, the valve pits came on the top, the opened the inspection hatch, and they could do 90% of the maintenance from the top of the pit without having to get in. Now of course that meant the operator was on his knees and he was bent over, but there was no heavy lifting involved. It was quite straightforward and this made life a lot easier.
And as you can see in this other one here, this is another station with some 300 millimeter vessels. You can see on the picture, on the right, just some sunlight coming down and that was the inspection hatch that enabled the operator to do the bulk of the work from the top. Now it doesn’t mean that the operator never has to come into the pits, to do a major shutdown they’ll have to lift the lids and get in there and do it and that’s all was possible to as well. But for the bulk of the maintenance that happened the soon, over that 10 years, we don’t want to get in the valve pit and this is one of the ways of doing it. So there are, if you’re doing risk analysis for this type of thing that are risks with doing this, here we can see on the left-hand side, on the right hand side, we were using flexible high-pressure nylon tube and that worked really well. Or you can do it in copper and stainless steel. Some of the issues that can happen with this I’m an operator might get in the valve pits and jump or stand on the nylon tube and it comes away and a valve opens. So this is shown in a fairly crude form.
Of course you can see on the right hand side, the, of the tubes are in a conduit. So they’re protected to stop that set of situations. So I’m showing the good on the right to the bad on the left, that minimises that risk and the risk of something else going wrong. And one of the things that we are always happy to do is it to have, when you do a risk analysis on one of these stations about what potentially can happen and go wrong, we’re very good and we have the experience in being able to assist you with that and stuff, too.
In many instances, they take it to the next level. So here we can see three stations, some with a multitude of valves below ground, but they’ve actually moved the entire controls to above ground and cabinets. And this is becoming quite common.
So what we’re going to see above ground as a nice environmental green cabinet with, which really isn’t gonna have any noise issues to it, everything’s accessible. We can see it all there. The one thing that I would say about above ground cabinets, if you don’t really have the experience in designing a cabinet to remove a pilot, to check on one of the fittings, it can be challenging because you need small fingers and sometimes the contractors put it in a fairly tight cabinet; it’s quite small and compact, I’ve got pressure transmitters in the everyday air valves. I’ve got other components that might leak onto the electricity. So there’s lots of. Good design things that we can assist you with. We even build above ground cabinet backing boards with all the components on it, we do it. But there’s a lot of pros and cons of doing this and experience as one of the keys to getting this and doing it right. A lot of the time, you can see the control tubes running down to the valve. So this is another possibility and something that we can discuss with you, if you’re interested in that design ensures that someone’s not on their knees working below ground, where they’re working at a safe working height.
So it’s, thinking about an operator’s back and they’re not bent over and doing sort of work that’s difficult. You can see the one in the middle here operating three valves. It’s quite complex. It looks like a lot of tubes there and a lot of filters and components. It can be a little daunting when you look at this stuff too, as well as pros and cons on all of those assemblies, but that’s something to consider.
I frequently get asked the question: do we need to put a strainer before the pressure reducing valve itself. So I’m talking here about not in the control lines, going to the the pilots, et cetera, but this is a main line strainer before a 300 millimeter valve. Now, one of the aspects of the bare med 700 series valve, the Y pattern design is very functional in that the bottom end of the actuator.
And we can see in the picture on the right-hand side here. Being a Y pattern almost straight through tight design means that if we have debris stones, construction debris, or anything that comes across, the possibility of having blockages reduced by having our designed valve, cause we don’t have lower bearings, we don’t have guide stems in the bottom and solids contained to pass.
So typically we don’t generally need a strainer beforehand, but why would you consider one? Or why would you give it thought to put one in? Here we can see some stations on rural water that we were using with some large strainers before.
We can see, of course that these strainers are quite large. They’re bulky, they’re expensive. In an overly expensive, but it’s taken up more room inside the inside of the cabinet and everything else. But why would you want to consider actually using a strainer? So I’m just going to one bit too far. I’ll start that one again.
I’m just going to go through this again and restart this particular one. Okay. That’s good. I’ve actually forgotten what it was. Okay. So I’ll go back to this one. So the next aspect to a pressure reducing station, is we frequently get asked the question, do we need to put a large strainer in before the pressure reducing valves?
I’m not referring to the little line strainer we use in the control line for the pilots, et cetera. But this is for the, in the actual pipeline itself. Do we need to put a strainer inside the valve itself? Now, the Bermad 700 series Y pattern type design is really practical and generally doesn’t need a strainer.
The why patent type design you can see in the picture on the right hand side, there has no lower bearings or guide stems. And if a solid was to come through, there’s a high probability that will simply pass through into the network rather than jamming in the bottom of the valve and keeping the valve open.
But there are many reasons why you may want to consider putting a strainer in and here we can see some strainers fitted in a roll water situation where we had some large strainers before the PRV. Okay. What this did is that it of course makes the station a little bigger, slightly more expensive, and it becomes a bigger process.
So why would you consider using a strainer? And these are some of the things that I think are probably critical. It’s all about getting back to that risk analysis again, if this was what we called a critical stations. So, this is supplying a very old network of AC pipe or fragile pipe, that’s subject to cracking or breaking if you have pressure variations. Sometimes if we have lumps of concrete that came off the liner of the main and jam the valve open, and the valve didn’t shut down and that could be catastrophic to a network. It could be raw or untreated water. So like this picture on the right hand side, this wasn’t using drinking water, but it was using untreated river and dam water.
And we had, there was a potential to get things like eels, construction debris, anything. Like we can get yabbies or fish that might jam inside the valve and might make the valve malfunction. One of the big things is that if you’re working on a brand new installation where there’s a lot of new infrastructure beforehand, a lot of new pipe work going in, let’s say they were using poly pipe or they’re using any nature of pipe that could be poly shavings. tHat could be any construction debris that was done through the construction or laying of the pipe. And if that got into the valve it could be catastrophic for the downstream network. So one of the things to be really careful of is to ensure that if we think there’s an element of risk of that, we may want to put that strainer in there.
Now, usually it generates very little of any head loss, but naturally it will gain more head loss if it starts to block, but it’s there as an insurance policy. So if you’ve done a risk analysis and you’ve decided and said “look, we want to minimize that risk. We want to ensure I’m for the little costs that it does. Let’s do it now and safeguard it”. That’s fine. And that’s up to the operator, but generally it’s not required in most installations. So the water was clean. I don’t need a strainer. And I’ve heard that many times before this picture you can see in the center was one particular picture. I took on a new installation and I had to come out, “Colin, the Valve’s not working”.
I pulled out bits of it looked like tubing. There was poly shavings that was rags in there. And I’m really not exaggerating. When I say this, having been commissioning valves for the last 30 years, what you’re seeing in the left-hand side, there is some of the things that we’ve seen in Valves. We’ve seen poly shavings, pipe, gaskets, rock, timber, grit concrete pipe linings come off. We’ve had multitude, unfortunately of animals, Platypus, eels, fish, turtles, wombats, sheep, possums. We’ve had, sometimes if the pipes has been constructed and it wasn’t capped off overnight, we’ve we had sheep, we’ve had wombats and it’s terrible. They’ve ended up in the valves as shown here and poly shavings and the strainer and stuff too, as well.
So the key thing about this is that I’m not trying to scare you into saying you need to put a strainer in, it’s something else that has to be maintained. It’s all about risk. If your stationed design was such that we’re going into a brand new network, we’re only dropping 10 or 15 meters across this PRV.
If we did have a situation where something had, it’s not catastrophic and it’s going do it. Okay. So let’s keep it simple, not put one in, but if the risk analysis says, look, the water’s going to be clean, constant drinking water, but we’ve had it so many times where we’ve had people maintaining a road and little lumps of concrete have come off the inside of the pipeline and jammed under the valve.
If it was untreated water we’ve, we’ve had turtles, fish, eels, that suck up against the valve and create issues inside the valve. So, it’s a matter of if the cost of the valve jamming open was going to be substantial because it would cause downstream pipe breakages, et cetera, et cetera, maybe the small investment and putting a strain on beforehand is worth it. That’s not for me to tell him, but for you to think about and determine whether that’s going to be practical or not.
Now, one of the really critical aspects to coming above ground or even below ground is the issue of, do I need an air release valve at the installation and is it important and where do I put it, and what type of valve should I use.
When we’re designing any pipeline, we generally don’t want any inclusion of air inside a pipeline at all. Why? Because it’s compressible. One of the facts of the matter is that when you reduce the pressure and the pipeline either comes out of solution. So if that air comes out of solution and follows the pipeline and follows up to them on the release valve, further down the track, happy days. But air constantly comes out of solution when you reduce the pressure. And the greater the differential pressure, the greater the flow rate, the more that becomes an issue.
When that air collects on the downstream side of a valve or collects at a high spot it’s potentially collapsible. And when it’s collapsible, that makes a pressure reducing valve on a hunt and carry on and make it not a great option.
So the thing is I would strongly recommend if you are putting an air release valve or thinking that putting any valve, speak to us about where we think we want to do it.
As you can see in the picture on the left-hand sides of the large station, you have under construction, you can see valves, back on the downstream side and some on the upstream side.
Now some people say look, if I put it on the upstream side, I’ve any air going into the PRV and that’s true. But if air comes out of solution on the downstream site under a lower pressure zone, that’s where it accumulates and creates an issue. So being able to automatically release that air downstream is critical for a pressure reducing station. It’s a very small capital investment, but it’s a long term investment and ensuring you get very good performance.
The type of valve you use downstream needs to have an automatic function or needs to be a combination of the valve or combination valve it’s search protection. It needs to be a valve that can automatically release that entained air to ensure that the valve’s not going to hunt because they’re regardless of brands, nature, and design, this might not be an issue when you first set it up or you set up the situation, but it’s going to accumulate and get worse as time goes on. And we’ve seen this in many instances before.
If you’re putting valves above ground, the question has always been, so where do we locate that air valve, Colin? Do we put it on the band going downstream, or I’ve seen this type of situation here. This is with a major water company by putting a collection team.
If you look at the picture on the left-hand side, you can see it’s got a T on the upstream side with pressure transmitters and the native valve, and one on the downstream site as well. This is really good designs in my opinion, why? Because the air has got only one place to go when it comes out of solution downstream, that’s the vertically upwards and into the air valve.
If you’ve got a long radius band elbow in the downstream side, do I put it at the high spot or do I put it on the base? And there are good design principles of what to do that. And we can assist you with whatever your design looks like to consider where to do it. But in these two instances that you can see in the picture here that categorically won’t be an issue with entrained air, making a valve bounce and create an issue with insufficient performance downstream if the air valves are connected like this.
Now that might not be practical in all instances and to put a T in rather than a long radius band is not always the best hydraulic solution, but if the velocities are modest and it’s not creating undue turbulence is a good solution, in my opinion.
The next question has been: do I need a pressure relief valve located downstream of the pressure reducing valve now?
Now, theoretically, a pressure reducing valve, its main function is I want him to maintain a constant pressure downstream regardless of upstream pressure and then regardless of. So, if the valve is configured correctly and it’s doing its job, you really should have no real need or risk to put a pressure relief in, if it’s doing its job well. But there are external influences that really affect what can happen in the pipeline downstream of the PRV can’t react to. So in some instances, it’s going to be worth considering this.
So let’s have an example here. We set the pressure, reducing valve up to respond at a certain flow rate. We have needle valves and speed controllers that ensure that we maintain a constant downstream pressure of plus or minus one or two meters and it works beautifully. But let’s assume downstream, there is a potential for a fire. If a fire department comes along and open up hydrants, they’re interested in one thing only and that’s opening up the hydrant, getting water and putting out the fire and switching it off. Are they concerned about what a hammer and closing valves slowly? No. They’re interested in putting out the fire.
It could be a case of there is an altitude valve downstream filling a reservoir, and the valve is filling it too fast rate and shuts off too fast. Now, if that altitude valve is five kilometers away from the PRV and we were using steel pipe, if they shut it off too quick and the generator pressure surge, it could be five seconds or 10 seconds before the PRV sees that high pressure and it’s all too late. Depending on the severity of the wave speeds inside that pipe, f it’s a kilometer per second, or if it’s 200 meters a second, that’s going to affect it. Now, the PRV can only respond to the pressures at the valve. It can’t respond to what’s happening five or six kilometers down the track. So if it’s a critical station where we really don’t want to see high pressure surges caused by operators or something happening downstream, it’s a good move to put a pressure relief valve in.
Sometimes downstream of a PRV you might have a pump station and that pump station might start and stop to fill a reservoir and the water runs through this PRV that is feeding. So all of a sudden we might see a very rapid increase in flow in a rapid decrease in flow, and those pumps start and stop. So unless the pump people control the rate in which the pump open and close at a controlled rate, the PRV might not see the constant downstream pressure, so it might be safe to put a really fast, even if that’s the case.
If it’s what we call a critical pressure reducing station, so this is something that’s gone into a very old network, very sensitive network that really can’t take much differential pressure and it doesn’t want any changes, it’s a good amount of insurance policy to make sure if something does go wrong with a PRV, it’s there as some insurance.
So again, it comes back to the SWAT analysis of, or the risk analysis of that the PRV look, if something goes wrong and it breaks the pipe, the cost on a small pressure relief valve is maybe a good inclusion. And we can give you a good idea on how to size it and to how to determine where to put the water and what it’s actually going to do.
One of the biggest things which really affect PRV stations is operators which have not been given good education. So these control valves can be a little daunting to operators sometimes and if they are… I can remember one of the water companies saying to me, one of the times that we tend to see breakages is our Pipes down streams. When operators do maintenance on the PRVs because some of the team that we use, haven’t been given the very latest training and overconfident in getting it right.
So when they bring the PRV online, they make a mistake and over pressurizes and creates an issue. A pressure relief valve is a good way to, to make sure that doesn’t create an issue. So if they do make a mistake, it’s a bit like saying, look, I’ve got the very best operators they’re well-trained, but one small mistake by closing or opening one valve in the wrong sequence might cause an overpressure condition. The relief valive is there to safeguard you.
In my opinion is a good idea and we can give you an idea how to size it, where to put it, where to distribute the water and how big does it need to work in what size they’re going to be. So we have a lot of experience in using it. I would say, I actually can’t tell you what the exact percentage of PRV stations have relief valves. It’s not a great deal, but it’s all deemed about risk and we can assist you with that risk. If you think you need one.
Okay, so, very important that valves are able to be isolated and be maintained. So here we can see a variety of different installations where we’ve got a butterfly valves or gate valves before and after valves that give us the possibilities to isolate the valve and to ensure that we can remove the internals of the valve and actually do some maintenance.
Some products mean that you can’t use butterfly valves, cause it might impinge on the surface of the valve or do something. You can see the velvet, the pitcher on the bottom left-hand side using butterfly valves. And in many instances, the one on the bottom right-hand side shows the butterfly valve heart up against the Bermad.
Now is it good practice to put it up against the side of the valve? It’s not a big deal. You can do it. It’s practical. It can do it. But the thing is that it’s sometimes it’s good to have a gap there that just gives you…what we don’t want with a pressure reducing valve is highly turbulent water coming in and out of the valve and having it just spaced a small amount distance away is a nice thing to have, but it’s not always exactly needed.
Sometimes it creates a straightening effect. If the valve is fully open, then it creates us a bit of a straightening effect as well. But the point is that you can use gate valves or butterflies on there. The important point here about the designers is to ensure that you have the ability to isolate them. There’s been many instances, we’ve been to jobs where there’s an upstream isolation, but there’s nothing on the downstream side. So they’ve had to drain section of the pipeline out to enable you to get to it. So the point is, it’s not so much about the design of the valve.
Gate valves are often used because they can’t close quickly, so we don’t want to generate water hammer if there is large flows. Butterflies at a little faster to close, but if there were a gear operator it can be slow too as well. But the key point to use a designer is we would like, ideally, to be able to isolate the valve on both sides to do major service on the valves; that might be every 10 years or 15 years, and that’s the point of this slide.
So in summary, when I look at some of the designs on the right hand side in there, we can do a multitude of different functions on these valves. The good thing about these diaphragm actuated control valves is that we can do this picture, on the top here was on a very high risk PRV that had a multitude of different safety factors, and the risk analysis basically said: we want to limit the flow, we want to have an over pressure guard, we want to have Judy and Stein buy large filters. We want a flow control system. We want all sorts of functions in there that says, look, we just cannot afford to have failure downstream and that’s fine. We can do all of those things, but the thing you always have to come back to is, and we do very good training on our valve, how daunting to some of those valves look to an operator.
So in my opinion, we’re practical, we are possible. We like to keep the design as simple as possible. We’d like to keep it as uniform as possible. If a company is using a multitude of valves, if we have the valves in a uniform build configuration and design is good for the operators, it’s familiar. I can come to this valve and see it, understand it. I know how it works, but when sometimes when they see this and even me after many years, I look at this and I still get sweaty palms thinking about how to maintain this. Because there’s a lot of brains all working at once in there. And if you don’t quite understand it and you may have the training at some time, it can be an issue.
So as a designer, the best thing I would suggest is trying to keep the system as simple, as practical or as possible. One of the things that we’ve found has been one of the most successful things when I’ve designed a station is made, is that the designer talks to the operations department, as well as the design team. When you get a lot of experience from operators that say, look, that’s a nice design, but I’m not going to be able to maintain that. This is what we’d like to do to be able to make it easier, and I think a good team that talk to one another about what’s important for the design to keep the cost down, but what’s practical to maintain is really good if they are talking to one another, and getting advice from their own operators too, as well.
But the most important thing is, if you can gather as much information about how the system’s going to work now, and in the future before the design is implemented, that’s the key to success. So many times when we get to a station, they send you the flow rates: it’s going to be up to 40 liters a second, maximum pressure is going to be a hundred meters, we want to reduce to 20 downstream. What can you give us, Colin? I can give you something with a snapshot of that, but can you give me an idea of what it’s else that’s going to do? Because when the valve doesn’t work and we didn’t have that information, it means that we just didn’t have the right information to make the right design.
So one of the most important things from my perspective is, when we’re designing anything, talk to us, give us a call and, or go back in this seminar and look at some of those information on the things that make our life and make hopefully the design a lot better. So by gathering that information, it’s really critical.
The thing that we find is that we have a very good relationship working with our customers. We have state offices in every major place, get to know the person who designs operates and trains your operators. We are very proud about what we do and we really like to make sure the design works well.
So good communication with your local Bermad office hopefully it’s going to make your design of a pressure reducing station a success.
So thank you very much for taking the time to watch this seminar. I really hope that you are able to gain some of the practical experience, which we’ve had over 30 odd years in working in pressure reducing stations.
The key advice I’d have for you going forward is that we have many offices throughout Australia, contact us at any of our state offices and speak with us, and we’re happy to share our experience and hopefully come up with a good design that works well for you. Thank you very much for watching.
-
Colin has more than 40 years’ experience working in water supply and irrigation in Australia, including 24 years with BWT. He credits his training at Weir pumps in his native Scotland for providing him with a solid grounding in engineering.
Colin is a mechanical engineer and a fitter and turner, who prides himself on taking a hands-on approach when designing and implementing successful installations across all aspects of BWT’s products and markets.
Read more about Colin: Who’s who at BWT – Colin Kirkland